干法制砂石粉含量
2024-03-24T13:03:11+00:00

研究探索:干法机制砂石粉含量对混凝土工作性能和力学性能
网页2023年1月5日 与湿法制砂获得的机制砂相比,干法制砂得到的机制砂石粉含量和含泥量均较高,且颗粒级配较差。机制砂颗粒岩性为石灰岩时,石粉具有一定的活性。鉴于此,本文对3 种厂家生产的干法机制砂进行研究,研究不同石粉含量对 C30 和 C50 两种强度 网页2020年9月15日 6种石粉控制技术及设备如下: 1、给料振动篦条筛 机制砂中的泥质含量升高会导致需水量加大,影响混凝土的强度,从而对其抗压能力造成一定影响。 因此,原 干法制砂工艺中,石粉含量多怎么办?6种石粉控制方法快来

机制砂怎么做到绿色环保?干法制砂生产工艺流程及设备配置
网页2020年6月22日 01干法制砂生产工艺流程 在北方干旱、少雨,水资源缺乏的自然条件下,优先采用干法工艺生产砂石骨料。 随着技术的进步,长期困扰干法生产的泥土、风化 网页2020年3月30日 湿法制砂主要针对于河卵石等含泥量较大的原料制砂,可有效降低含泥量,但细砂流失严重,且需充足水源。 干法制砂主要针对以山采碎石为原料的制砂,细砂 机制砂生产线的工艺分类 知乎

干法制砂VS湿法制砂,各有什么优缺点?如何选择?听听
网页2022年4月2日 主要优点: (1)成品砂石骨料外观好。 (2)生产过程中泥土和石粉被水流带走,不产生粉尘,避免空气污染。 主要缺点: (1)消耗大量水资源,吨砂石料约 网页2021年2月26日 绿色矿山干法制砂工艺在近年逐渐普及,楼式制砂是目前干法制砂先进的技术形态,但石粉的控制却是决定机制砂成品质量及产量的重要方面。 机制砂中石粉存在 【砂石骨料】干法制砂工艺中,石粉含量多怎么办?6种石粉

江苏吉地达:干法制砂新工艺,别让粉尘“跑了”!
网页2023年4月22日 2、干法制砂的缺点 干法制砂生产过程中粉尘含量大,易造成空气污染,需要进行洒水、喷雾等一定的降尘处理操作。 干法制砂原材料要求高,原料是否干净,会 网页2023年4月25日 机制砂的质量控制从原料的选择上就要加以选择控制,以生产出符合规定的砂石骨料,尽量选择泥土、轻物质等杂质含量少的母岩。 2、合理选择工艺设备 根据当 如何生产高品质机制砂?制砂楼助力机制砂生产!骨料

干法机制砂生产线工艺流程及视频利弊分析河南红星机器
网页2023年4月24日 干法制砂与湿法制砂哪种工艺好?其实各有优缺点,主要看哪种方式更适合,下面为大家介绍干法制砂的利弊,供参考。 优点: 1、机制砂水分含量低(一般低 网页2023年3月21日 在干法制砂的过程当中,倘若想抑制石粉不发生外溢及四处飞溅,需要对整个生产线设备进行全封闭加工模式,再搭配袋式除尘器和粗细粉分离工作机等设备对石 干法制砂设备中石粉怎么处理?工作生产砂石
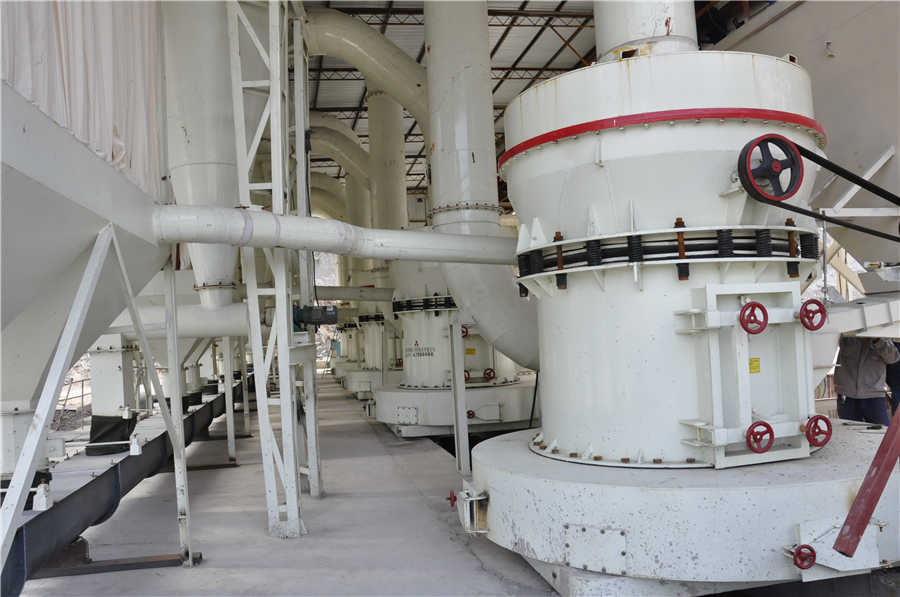
干法制砂实现环保生产,背后的制砂工艺和技术都在这了!机制
网页2020年9月25日 5)采用干法生产时测定风机送风量,经调试运行正常后固定风量,使生产出的机制砂石粉含量控制在相对稳定的状态。 补充: 采用湿法生产时,测定用水流量及洗砂机的倾角,在洗去石粉的同时,避免较大颗粒的砂被洗掉,造成级配不符合要求。网页2022年4月2日 主要优点: (1)成品砂石骨料外观好。 (2)生产过程中泥土和石粉被水流带走,不产生粉尘,避免空气污染。 主要缺点: (1)消耗大量水资源,吨砂石料约耗水2~35t,制砂过程中产生的泥粉污水如果直接排放会造成环境污染,回收利用又需要增加大量 干法制砂VS湿法制砂,各有什么优缺点?如何选择?听听
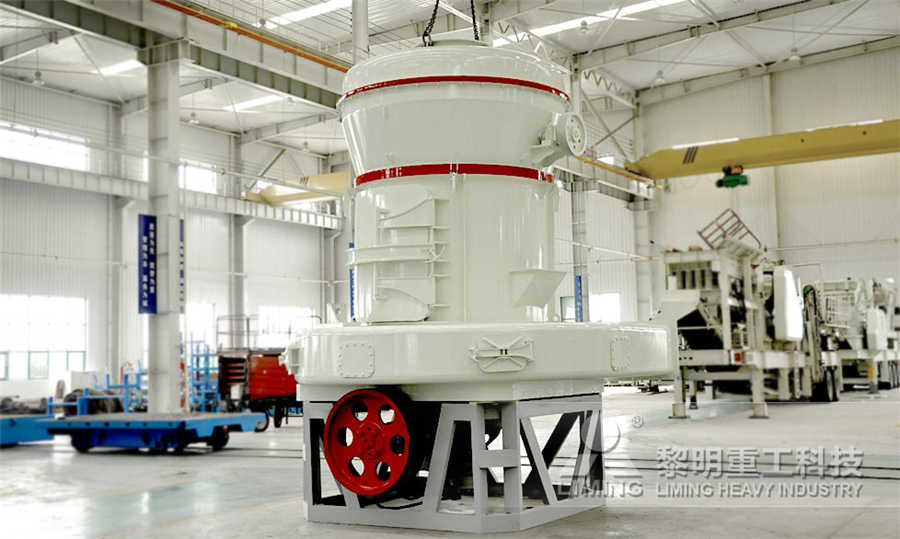
机制砂生产线的工艺分类 知乎
网页2020年3月30日 湿法制砂主要针对于河卵石等含泥量较大的原料制砂,可有效降低含泥量,但细砂流失严重,且需充足水源。 干法制砂主要针对以山采碎石为原料的制砂,细砂无流失,石粉含量可控,砂子级配更合理,但对原材料的含泥量要求严格。网页2022年7月8日 干法制砂工艺,即在砂子生产过程中,对于砂子中的泥粉进行洗出的过程不需要水,因此称之为干法制砂工艺。 在对石料加工过程中,由于激烈的碰撞以及石料本身有一定的含土量,使得机制砂中含有一定的石粉和泥粉。采干法、湿法及半干法制砂工艺介绍Hl生产线破碎机机制

如何提高砂石质量? 知乎
网页2021年7月22日 干法制砂要选择具有变频调速的细粉分离器或除尘器风机转速,能够调节成品砂中的石粉含量; 湿法制 砂要合理选择洗砂机中的冲洗水水量和洗砂机螺旋转速。七、干法制砂模式 1)当生产高性能混凝土用砂或干混砂浆免烘干机制砂时,制砂母岩在 网页2023年4月22日 2、干法制砂的缺点 干法制砂生产过程中粉尘含量大,易造成空气污染,需要进行洒水、喷雾等一定的降尘处理操作。 干法制砂原材料要求高,原料是否干净,会影响成品砂的质量,因此需要严格控制砂石中泥土和有机物等杂质的含量。 新型干法风选脱粉制江苏吉地达:干法制砂新工艺,别让粉尘“跑了”!

机制砂生产技术与质量控制 豆丁网
网页2021年11月24日 干法制砂生产 的机制砂石粉含量往往更高,质量一般都能满足或者高于标准,这时应考虑选 用选粉设备如选粉机分离多余石粉或部分湿式生产,洗去部分石粉,从而满足 标准要求。 机制砂石粉的流失在湿法制砂过程中更加明显,想要满足石粉 网页2020年5月28日 半干法生产工艺相对湿法生产工艺,最大特点就是用水冲洗掉制砂原料表面的泥和石粉,成品砂部分或全部不再进行水洗,因此用水量相对少多了,成品砂中石粉流失量少了,水份含量较低。 但这种砂石生产工艺还需较多的水资源,污水处理装置仍须配备 机制砂生产工艺的湿法、干法、半干法,哪种更适合你的制砂
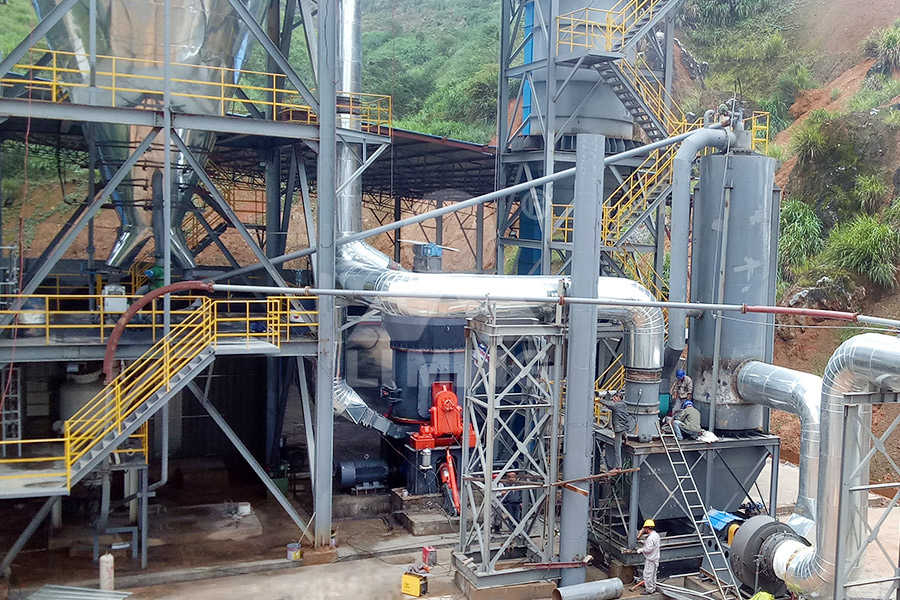
干法制砂产尘严重,污染环境很苦恼?案例介绍机制砂的防尘
网页2019年10月11日 腾讯内容开放平台 干法制砂产尘严重,污染环境很苦恼? 案例介绍机制砂的防尘措施 工程机械视点 干法制砂不受水源和环境的限制,在水资源匮乏的地方也可以进行,减少水资源污染。 另外,干法生产只除去小于75um的颗粒,各种颗粒级配 网页2023年4月22日 江苏吉地达:干法制 砂新工艺,别让粉尘“跑了”! 江苏吉地达机械制造有限公司 点击19次 前,我国大多数地区应用的是天然砂,随着改革开放的深入发展,基本建设的日益发展,砂石用量不断增多,由改革前的6亿多吨增加至15 江苏吉地达:干法制砂新工艺,别让粉尘“跑了”!

干法、湿法及半干法制砂工艺介绍Hl生产线破碎机机制
网页2022年7月8日 干法制砂工艺,即在砂子生产过程中,对于砂子中的泥粉进行洗出的过程不需要水,因此称之为干法制砂工艺。 在对石料加工过程中,由于激烈的碰撞以及石料本身有一定的含土量,使得机制砂中含有一定的石粉和泥粉。采网页2021年11月24日 干法制砂生产 的机制砂石粉含量往往更高,质量一般都能满足或者高于标准,这时应考虑选 用选粉设备如选粉机分离多余石粉或部分湿式生产,洗去部分石粉,从而满足 标准要求。 机制砂石粉的流失在湿法制砂过程中更加明显,想要满足石粉 机制砂生产技术与质量控制 豆丁网

机制砂石粉含量过多应该如何解决?GSY13 哔哩哔哩
网页2022年3月27日 三、如何控制机制砂中石粉含量 1、机制砂入料尺寸要合理 机制砂物料的入料尺寸要符合入料标准要求,如果尺寸过大,制砂机无法进行破碎,就会导致机制砂石粉含量增多,严重时还会损坏制砂机。 2、 网页2022年3月31日 目前砂石干 法和湿法工艺存在较大的争议,主要集中在以下两点:一是湿法工艺可以有效清除砂石中的泥粉,确保成品的饱和面干,且控制粉尘容易。但备件损耗大,用水量较大,且增加了水处理的成本。因为中水回用将导致成品絮凝剂残留,不 砂石生产工艺干法、湿法大家谈 利用干湿工艺优势 做好砂石

机制砂生产线的工艺分类 知乎
网页2020年3月30日 湿法制砂主要针对于河卵石等含泥量较大的原料制砂,可有效降低含泥量,但细砂流失严重,且需充足水源。 干法制砂主要针对以山采碎石为原料的制砂,细砂无流失,石粉含量可控,砂子级配更合理,但对原材料的含泥量要求严格。网页2019年1月4日 其投资费用比湿法少,比干法多,成品砂石粉含量介于二者之间,运行成本也在二者之间。 半干法生产工艺最大的缺点就是,在预筛分处进行冲洗,进入立式制砂机的造砂原料,水份含量在610%,制砂机成砂率较低,筛分困难。湿法、干法和半干法制砂,3种制砂工艺经济对比及优缺点分析

江苏吉地达:干法制砂新工艺,别让粉尘“跑了”!
网页2023年4月22日 2、干法制砂的缺点 干法制砂生产过程中粉尘含量大,易造成空气污染,需要进行洒水、喷雾等一定的降尘处理操作。 干法制砂原材料要求高,原料是否干净,会影响成品砂的质量,因此需要严格控制砂石中泥土和有机物等杂质的含量。 新型干法风选脱粉制网页2023年2月17日 2成品砂品质好 楼站式制砂系统集制砂、粒型优化、石粉控制、级配调整、含水率控制于一体,机制砂石粉含量有级可调,可以安装在线机制砂检测系统和拌湿机,及时调节机制砂质量,同时可以防止成品砂离析,专用于精品机制砂生产。楼站式干法整形制砂加工工艺有哪些优势?生产系统机制

如何提高砂石质量? 知乎
网页2021年7月22日 干法制砂要选择具有变频调速的细粉分离器或除尘器风机转速,能够调节成品砂中的石粉含量; 湿法制 砂要合理选择洗砂机中的冲洗水水量和洗砂机螺旋转速。七、干法制砂模式 1)当生产高性能混凝土用砂或干混砂浆免烘干机制砂时,制砂母岩在 网页2023年4月22日 江苏吉地达:干法制 砂新工艺,别让粉尘“跑了”! 江苏吉地达机械制造有限公司 点击19次 前,我国大多数地区应用的是天然砂,随着改革开放的深入发展,基本建设的日益发展,砂石用量不断增多,由改革前的6亿多吨增加至15 江苏吉地达:干法制砂新工艺,别让粉尘“跑了”!